Rock 541 Petrochemical
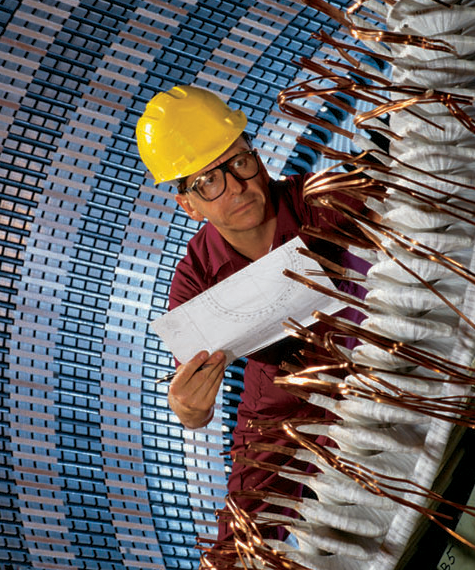
Petroleum / Chemical Motors
Each year brings a new and stronger challenge to the petroleum and chemical industries to be more competitive. TECO-Westinghouse recognizes motors are a significant part of the competitive solution. The petroleum and chemical industries require efficient, reliable, and life cycle cost effective motors and generators.
The TECO-Westinghouse Rock 541™ Motor meets these challenges.
The Rock 541™ is a motor custom designed for your specific application requirements. It combines features developed during 100+ years of experience with the latest design technology. The Rock 541™ Motor can meet or exceed the most demanding specifications. The Rock 541™ Motor can meet the lowest vibration requirements, and is available in all API 541 configurations. It provides you with state of the art technology and performance and, just as importantly, keeps you within budget.
TECO-Westinghouse utilizes the latest design and management tools to produce the Rock 541™ Motor to the highest quality standards. Systems that support concurrent engineering, 3D solids modeling, and finite element analysis are employed. These engineering tools are coupled to one of the most advanced product data management programs to insure product integrity.
Whatever your requirements, the TECO-Westinghouse stands ready to assist you in developing a solution.
Features
Features:
Included for all Rock 541™ general purpose motors | |
2.1.2
|
Motors are designed for continuous operation or long periods of inactivity in petroleum / chemical plant environments. |
2.2.2.2
|
Motor winding brace system designed to substantially exceed 5,000 full voltage starts. |
2.2.6.2
|
Three cold/ two hot starting duty. |
2.4.5.1.2
|
Two pole motors utilize one-piece, heat treated forged steel. |
2.4.5.2.5
|
Connection of rotor bars to end rings through approximately 10,000HP is via induction brazing. |
2.4.10.5
|
Screens will be stainless steel. |
2.4.10.6
|
Fan systems will be non-sparking. |
2.4.10.7
|
Minimum stator core plate material will be C5. |
Available for all Rock 541™ Motors | |
2.1.3
|
Lower than conventional noise levels. |
2.1.7
|
Motors are available for hazardous locations. |
2.4.5.1.4
|
Shaft Forgings are ultrasonically inspected. |
2.4.6.1.3
|
Damped unbalance response analysis. |
2.4.6.2.1
|
Three plane balancing of the rotor. |
2.4.9.5
|
Testing with contract coupling and idling adapter or mass moment simulator. |
Some above and beyond API 541 requirement | |
2.3.1
|
A single VPI treatment of the stator will meet the requirements of this paragraph. The Rock 541™ will receive a minimum of two complete VPI treatments followed by a durable coat of epoxy varnish. |
2.4.5.2.2
|
As an alternate to copper/copper alloy, cast and fabricated aluminum rotor cages are allowed by this API paragraph. The Rock 541™ cage material will be premium copper/copper alloy only. |
2.4.5.2.3
|
Jointed rotor end rings are allowed at some speeds by this paragraph although it is noted that rings without circumferential joints are preferred. The end rings of Rock 541™ Motors do not contain circumferential joints at any speed. |
2.4.7.3
|
Conventional straight fit (liner to bearing housing) sleeve bearing liners are allowed by this paragraph. Sleeve bearing systems provided in all Rock 541™ Motors will be of the superior spherical seated self-aligning type. |
2.4.7.21
|
Various options are discussed for shaft/bearing seals in this API paragraph. All Rock 541™ sleeve bearing motors utilize nonmetallic, floating, self-aligning seals that exceed the requirements of this paragraph. |
For Unequalled Dielectric Strength and Voltage Endurance
Thermalastic® is a proprietary, integrated insulation system that impregnates the wound and connected stator with a solventless epoxy resin. Developed by Westinghouse over 40 years ago, Thermalastic® is acknowledged as the industry’s premier insulation system and is under continuous development to maintain its position as the world’s finest.
The bearing system used in World Series™ Motors has been designed and engineered for continuous, reliable performance and easy maintenance. Both anti-friction and split-sleeve bearings are offered. When required, bearing insulation can be added to either bearing type.
World Series™ Motors use box frame construction to provide frames that have the mechanical strength and stability to assure years of dependable, economical performance.
TECO-Westinghouse induction motor rotors are recognized as the most reliable in the industry, and their high performance standards are a hallmark of the World Series™ Motors.